Health, safety and environment
Industrial safety, occupational health and environmental protection
Participation in initiatives and programmes
The World Bank’s Zero Routine Flaring by 2030 initiative
UN 17 Sustainable Development Goals initiative
CDP climate programme
Global Methane Initiative
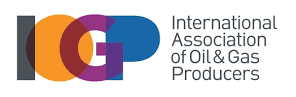
Caspian Environmental Protection Initiative — CEPI
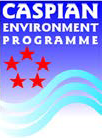
International Association of Oil & Gas Producers – IOGP
Performance highlights
Health, safety and environment management system
The health, safety and environment management system is designed to Kazakhstan’s statutory requirements, ISO 14001 and ISO 45001 international industry standards, global best practices and guidelines, and recommendations of the International Association of Oil & Gas Producers (IOGP). It covers ten areas and relies on four pillars: goal achievement, leadership, risk management, and continuous improvement.
Since 2006, KMG operates an integrated quality, environmental, and occupational health and safety management system compliant with ISO 9001, ISO 14001, and ISO 45001. KMG’s significant energy users are certified to ISO 50001. The effectiveness of the HSE management system is verified by independent auditors on a regular basis.
To improve its management system, KMG has its Health, Safety and Environment Management System (HSE MS) certified to ISO 45001.
The management system is designed to create an environment for managing HSE risks and opportunities. Its deliverables include prevention of injuries and health damage across KMG Group and ensuring occupational health and safety. That said, it is of vital importance for KMG to eliminate or minimise HSE risks by taking effective preventive actions.
In 2023, the Group updated and approved the Guidelines on Health, Safety and Environment Management System to improve its overall HSE management, in particular as regards:
- management responsibility for employee compliance with KMG Life‑Saving Rules;
- granting KMG Group employees a guaranteed legal right to reject or suspend work in case of a situation reasonably believed to be potentially threatening to health, safety or environment;
- designing and implementing the Group’s Employee Health Management Programme relying on health risk assessment;
- using Qorgau Cards to engage the Group’s employees and contractors in risk management, identification and notification of potential hazards.
To keep the management system documents up to date, KMG Group revised a number of internal regulations:
- Regulations on HSE Risk Management in Hazardous Operations;
- Regulations on Emergency Medical Care;
- Rules for Accident Reporting and Investigation;
- Standard for Provision of Workwear, Footwear and Personal Protective Equipment.
On 5 October 2023, representatives of KMG’s Management Board and Board of Directors, TCO, NCOC and KPO together with CEOs of 44 subsidiaries and associates took part in the Forum of KMG Group’s CEOs – Leadership in Shaping a Robust Safety Culture. JMJ’s global experts held a workshop on safety leadership, with TCO, NCOC and KPO representatives sharing experience in accident investigation and consequence management.
“KMG prioritises health and safety of everyone involved in its operations and maintaining environmental sustainability across its footprint. For us, these values are indisputable,” noted Magzum Myrzagaliev, Chairman of KMG’s Management Board.
Environmental responsibility and safety
2023 highlights
KMG Group’s goals in HSE management are directly related to its Development Strategy. KMG’s Development Strategy until 2031 covers strategic initiatives to promote greater environmental responsibility. KMG Group’s environmental priorities include management of air emissions, water resources and production waste, flaring reduction, and land reclamation.
Management teams at KMG and its subsidiaries and associates take a zero tolerance approach to losses and harm caused by environmental pollution. In reducing our air emissions, we focus on increasing raw gas utilisation while minimising flaring.
According to the approved Environmental Policy, the Company strives to achieve zero routine gas flaring.
In 2015, KMG supported the World Bank’s Zero Routine Flaring by 2030 initiative. Gas flaring reports under the Initiative are submitted on an annual basis.
The Company remains committed to being an environmentally responsible business, further enhancing its environmental protection management system, maintaining dialogue with all stakeholders on this matter, and thus delivering on its commitments as stated in the Company’s Environmental Policy.
To mark the World Environment Day, KMG held a conference in Atyrau titled “Atyrau Ecological Dialogue: Ecology and Industry. Partnership for the Benefit of Society”. During the event, environmental projects were widely discussed, as well as measures to reduce atmospheric emissions at the Company’s assets.
In support of the initiative of President Kassym‑Jomart Tokayev to plant 2 bln trees within five years, the Akymat of the Atyrau Region and KMG signed a Memorandum of Cooperation on the greening of Atyrau. In accordance with the document, Atyrau Refinery will plant 10 thous. trees along the Sokolok canal close to Talkayran within three years. In 2023, the refinery also donated 200 fully grown root‑balled ash trees to the Akymat. The trees will be planted in the retro park area.
As part of this initiative, about 300 employees of the Company took part in a corporate environmental tree planting event in October.
In September 2023, the Company sponsored an environmental challenge as part of the World Cleanup Day, an environmental campaign uniting millions of people who show care for nature by cleaning it from waste. This challenge was successfully replicated by KMG subsidiaries – OMG, KBM, EMG, MMG, Atyrau Refinery, PetroKazakhstan Oil Products, Pavlodar Refinery, CaspiBitum, KazGPZ, and OSC. As a result, over 900 tonnes of waste was collected across all regions, an equivalent of a five‑storey building.
In 2023, the Company established KMG‑Volunteer, a volunteering programme. As part of the programme’s Action Plan and in line with the President’s Address to the People of Kazakhstan, volunteers planted trees on the territory of Alikhan Bukeikhan school‑lyceum No. 76 in the country’s capital. KMG donated 129 trees to the school.
Priority environmental projects
Eliminating legacy pollution
Elimination of historical pollution, as well as sources of negative environmental impact (idle wells, wastewater reservoirs, landfills and other production facilities).
Reducing atmospheric emissions
Reduction in emissions through improved technology solutions, e.g. replacing fuel oil with fuel/natural gas used as a process furnace fuel, using next‑generation additives, tree planting and land improvement at production facilities, replacing equipment, expanding gas processing capacity, installing gas processing units, etc. Key emission reduction targets are to be set as part of a programme to bring down pollutant emissions.
Project: Tazalyq
The Tazalyq project provides for the upgrading of Atyrau Refinery’s wastewater treatment facilities as well as the reclamation of the Tukhlaya Balka evaporation fields.
Formation water desalination plant at the Karazhanbas field
The plant plays a strategic role in the region and is expected to make the field self‑sufficient in terms of water supply and free up significant amounts of water for local residents.
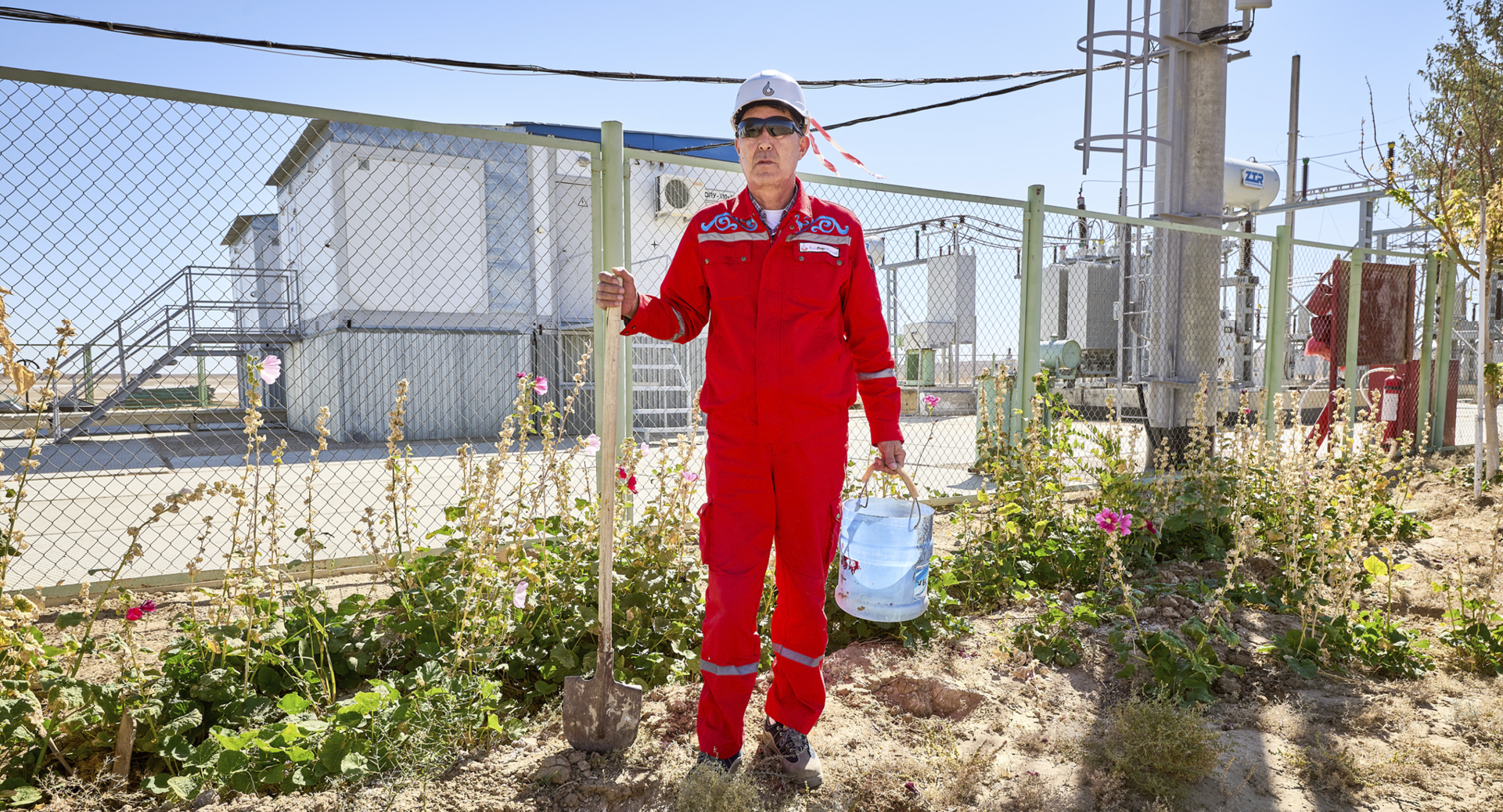
Automated environmental monitoring information system
The automated environmental monitoring information system is designed to create a shared information space in environmental protection and covers the following critical tasks: automated generation of environmental reports to government agencies; maintaining the database of authorisation regulations and calculating environmental emission fees; day‑to‑day environmental monitoring based on environmental controls at production sites.
Recovery of historical oil wastes and oil‑contaminated soil treatment
Complete disposal of historical oil waste and oil‑contaminated soil treatment through 2024.
Water Resources Management Programme
The programme is to improve the efficiency of water use and protection and identify measures and targets to reduce water withdrawal and water consumption, increase recycled water supply and water reuse, reduce discharges and adverse environmental impact in general for KMG and its subsidiaries and associates, and develop recommendations.
Employee training in HSE
People are our most important asset, so HSE training remains top of mind for KMG Group. Therefore, mandatory staff education, training and upskilling in occupational health, industrial and fire safety and environmental protection are priority training areas for KMG.
Starting from 2021, KMG’s Corporate Centre employees undergo mandatory training in occupational health and industrial and fire safety basics. The sessions are held on the platform of KMG Engineering.
In 2023, KMG Group spent a total of KZT 938,991.09 thous. to train 108,464 employees, including HSE training in the following key business segments: KZT 482,964.4 thous. in the upstream business; KZT 143,839 thous. in the midstream business; KZT 196,533.5 thous. in the downstream business; KZT 110,614.9 thous. in the service business, and KZT 5,039.2 thous. in the Corporate Centre.
HSE training is performed according to the «70/20/10 — on-the-job training / internal training /external training» model rolled out across KMG’s existing training facilities/ centres. Mentoring and internal coaching programmes are implemented for long-service employees, with master classes and training sessions conducted as well as various contests to recognise the best performers, which enhances internal communications and motivates personnel to strive to excel in their jobs.
The companies that have their own training facilities/ centres include OMG (Zhanaozen), KTO (Aktau), Oil Services Company (Aktau), and KMG Engineering (Astana).
Using energy resources and improving energy efficiency
KMG’s energy saving and energy efficiency efforts are based on the methodology set out in ISO 50001 Energy management systems, an internationally recognised bestpractice framework for systemic energy management.
In December 2022, as part of its Low-Carbon Development Programme for 2022–2031, KMG approved the Energy Policy applicable to all its subsidiaries, associates and contractors.
The Policy supports energy efficient procurement and projects, defines roles and responsibilities in energy management, and promotes economically feasible best available techniques, international practices, standards and administrative resolutions to improve energy efficiency and saving. An integral part of KMG’s 2022–2031 Low-Carbon Development Programme, the Policy lays foundation for setting and reviewing energy-related goals and objectives.
In December 2022, all KMG subsidiaries and associates approved similar policies and aligned their internal documents with KMG’s Energy Policy.
In 2023, the Company approved the Regulations on Energy Saving and Efficiency in KMG Group. The Regulations set out an interaction procedure along with the scope of authority, responsibilities and duties of the Group’s units and employees as part of energy saving and efficiency management.
Energy consumption
The Company’s Corporate Centre collects and analyses energy consumption and energy efficiency-related data, monitors the dynamics, identifies opportunities for improvement, and conducts year-on-year and peer benchmarking (IOGP).
In 2023, total energy consumption amounted to 124.1 mln GJ (4,088 thous. tonnes of reference fuel), down 6% yearon-year, with the reduction in energy consumption attributable to the implementation of an Action Plan on energy saving and energy efficiency as part of the implementation of KMG’s Low Carbon Development Programme, including 12.9 mln GJ in electricity, 3.8 mln GJ in heat, 1.6 mln GJ in motor fuel, and 105.8 mln GJ in boiler and heating fuel (with oil refinery gas, natural gas, stripped gas and associated petroleum gas accounting for 24%, 22%, 15% and 9% of the total energy consumption, accordingly). The total energy consumption is divided among three business segments: Upstream, Midstream, and Downstream.
In 2023, KMG Group’s self-generated energy amounted to 740 thous. kWh in electricity and 3,988 thous. Gcal in heat
In accordance with the Rules for Determining the Tariff for the Support of Renewable Energy Sources, Atyrau Refinery purchased for internal use in 2023 from Financial Settlement Centre of Renewable Energy LLP 3,741 thous. kWh of electricity produced by renewable energy facilities. In 2023, PKOP and CaspBitum solar panels generated 101 thous. kWh of electricity for street lighting.
Reducing energy consumption
KMG Group’s key strategic energy saving and energy efficiency initiatives include process equipment upgrades, deployment of energy saving technologies, optimisation of heat generation and consumption, and the development of the Group’s own generation assets, including APG‑fired generation.
From 1 July 2023, the wholesale electricity market (WEM) was reformed by introducing centralised purchase and sale of electricity (single buyer mechanism) and a real‑time balancing electricity market.
Under the new mechanism, the same electricity tariff is set for all WEM consumers across the country, and WEM players will be financially liable for imbalances.
Some of KMG’s subsidiaries and associates already operate in the wholesale electricity market.
In 2023, 60 initiatives were accomplished as part of the Action Plan to implement the Low‑Carbon Development Programme. The estimated annual fuel and energy savings amounted to 653.2 thous. GJ, which in physical terms corresponds to 12,312 thous. kWh of electricity, 8,276 Gcal of heat energy, 2,489 tonnes of boiler and heating fuel and 13,149 thous. m³ of natural gas, an equivalent of 45,054 tonnes of CO₂ in emission cuts. Overall spending on the energy saving and energy efficiency initiatives was KZT 3,509 mln.
Energy intensity
In 2023, KMG Group’s energy consumption in the upstream sector averaged at 2.7 GJ per tonne of hydrocarbon production, still 80% above the International Association of Oil & Gas Producers (IOGP) average for 2022, i.e. 1.5 GJ per tonne of hydrocarbon production.
KMG Group’s average does not reflect the status quo because of a severe distortion owing to high energy intensities at OMG and KBM. KBM’s energy consumption per tonne of produced hydrocarbons is six times higher than the IOGP global average, as production at the Karazhanbas field requires the use of steam and hot water to displace oil from subsoil reservoirs. At OMG, the measure is 2.3 times higher than the IOGP global average as a result of high dissolved paraffin concentrations and the rheological properties of oil, which means that it needs to be heated during production and transportation in both winter and summer.
Renewable energy
In addition to energy efficiency and energy saving, the Action Plan to implement KMG’s Low-Carbon Development Programme places a special emphasis on renewable energy projects and the offset policy, which are expected to help reduce our carbon footprint.
KMG is doing a feasibility study to assess resources for the low-carbon production of hydrogen, technical, commercial and economic viability of investments in construction, and potential for blue hydrogen production with further СО₂ injection into oil and gas fields to intensify oil recovery
CCUS-enabled methods of blue hydrogen production is key to conforming with classification.
As a hydrocarbon production operator, KMG can produce hydrogen using steam reforming or pyrolysis of natural and/or associated petroleum gas combined with CO₂ capture and burying in accordance with carbon intensity requirements.
Management
KMG’s long‑term Development Strategy prioritises the following climate‑related initiatives:
- Greenhouse gas emissions management
- Reduction of routine flaring
- Improvement of GHG emissions intensity per unit of production and overall energy efficiency;
- Reduction of methane leaks
- Increased financing for green projects
The global trend to fight climate change is increasingly affecting companies across the world. In furtherance of the government policy on the low‑carbon development of the country, KMG has approved its 2022–2031 Development Strategy, which meets high safety standards and the sustainable development principles. According to KMG’s Development Strategy, gradually reducing the carbon footprint is one of the Company’s key priorities.
In addition to the Programme’s main focus on improving the energy efficiency of the operating processes and implementing renewable energy projects, the Company is also planning to implement additional decarbonisation measures, specifically: carbon capture, utilisation and storage (CCUS) projects, development of hydrogen energy, and implementation of forest‑climate projects.
In 2021, KazMunayGas approved its Low‑Carbon Development Programme for 2022–2031 with a focus on reducing direct and indirect greenhouse gas emissions by 15% vs 2019. Furthermore, this year KazMunayGas is preparing its 2060 Low‑Carbon Development Programme.
Risks and opportunities
The corporate risk management system is a key component of the corporate governance system, and is used to identify, evaluate, monitor and mitigate potential risks that may hinder the achievement of strategic goals. The Company implements a range of initiatives to minimise such risks, with risk reports submitted to the Board of Directors on a quarterly basis.
Information disclosure
In the CDP’s Climate Change Questionnaire, KMG discloses direct and indirect greenhouse gas emissions data, greenhouse gas management issues, and key risks and opportunities for all KMG assets, including international assets in Romania and Georgia, starting from 2019.
In July 2023, the KMG Climate Change 2022 Questionnaire was published. According to the report, direct carbon dioxide emissions in KMG Group totalled 7.6 mln tonnes of CO₂ (8.1 mln tonnes of CO₂e) in 2022. The CO₂ equivalent data are presented using the global warming potential ratios set out in the IPCC Fifth Assessment Report (28 for methane and 265 for nitrous oxide).
The greenhouse gas emissions data were verified by independent accredited organisations’ reports for each subsidiary or associate. Data for 2023 will be disclosed in KMG’s CDP report to be published in 3Q 2024. We seek to ensure consistency and comparability when preparing our disclosures. We are committed to enhancing disclosures and increasing the scope of reporting around our Scope 3 emissions.
Efficient use of raw gas
The reduction of gas flaring is one of the priority tasks for KMG Group. According to the approved Environmental Policy, the Company strives to achieve zero routine gas flaring. KMG is paying increasing attention to the responsible use of gas. Hence, over the last six years, routine flaring has decreased by 89% (2017: 315.8 mln m3). Utilisation of raw gas in 2023 was 98.9%. Flaring was brought down thanks to the launch of a gas processing unit at Embamunaigas, which provides highly efficient treatment of hydrogen sulphide. In addition, a modern gas processing facility with a capacity of 226 mln m3 of commercial gas per year was commissioned at Kazakhoil Aktobe’s Kozhasai field.
In 2023, raw gas utilisation rate was 98.9 %, with flaring at 1.4 tonnes per 1,000 tonnes of produced hydrocarbons (1.5 tonnes in 2022 and 2.1 tonnes in 2021), down 7% year‑on‑year and 84% lower than the IOGP industry average.
In 2015, KMG supported the World Bank’s Zero Routine Flaring by 2030 initiative. KMG strives to minimise raw gas flaring. Raw gas flaring reports under the Initiative are submitted on an annual basis to the World Bank’s representative office in Kazakhstan.
KMG’s production operations generate production and consumption waste. KMG Group develops and implements a set of measures to improve the waste management system, keeps records of waste generated and accumulated, including contractors’ waste, and performs the safe accumulation of waste until it is recovered or disposed of. In 2023, KMG’s expenses for the recovery of historical oil waste totalled KZT 17.8 bln.
It is important to emphasise that in selecting waste recovery methods, priority is given to modern technologies, including those that cause no secondary pollution of the environment.
On 6 August 2019, a memorandum of cooperation was signed between the Ministry of Ecology, Geology, and Natural Resources of the Republic of Kazakhstan and KMG with historical oily waste disposal and oil contaminated soil remediation commitments until 2024, inclusively. The memorandum covers MMG, OMG, and KBM.
Starting September 2019, inventories of contract lands were conducted to determine waste characteristics, the content of oil products in the waste, and the waste volume. On the basis of the inventories data, the relevant remediation projects for oil‑contaminated soil were developed and agreed upon with the government authorities, with safe and efficient technologies for oily waste disposal selected and recommended and schedules drawn up for oil‑contaminated soil remediation through the year 2024, inclusively.
In addition, although EMG and KTM are not covered by the commitments under the memorandum, they work to eliminate historical pollution too.
All of the above companies have entered into long‑term contracts with organisations specialising in the disposal of historical oily waste and clean‑up of oil‑contaminated soil.
In 2023, a total of 1,145 thous. tonnes of historical waste was disposed of at KMG subsidiaries’ and associates’ facilities, with their disposal sites remediated.
KMG Group’s Corporate Waste Management Standard was drafted and scheduled for approval in 2024. The Standard specifies step‑by‑step actions of officers in charge at subsidiaries and associates when carrying out waste management activities to ensure compliance with the requirements of Kazakhstan’s environmental laws. The standard is a guiding document for waste management at production facilities.
As part of introducing the separate collection and recycling of waste, in 2023 terminals (reverse vending machines) were installed in the KazMunayGas building to accept aluminium cans, plastic and glass bottles. In 2023, the machines accepted 17,516 plastic bottles and 3,403 aluminium cans for further recycling.
Oil and gas assets
Under the terms of certain contracts, in accordance with legislation and regulatory legal acts, KMG has legal obligations to dismantle and liquidate fixed assets and restore land plots at each of the fields. In particular, KMG’s obligations include the gradual closure of all non‑productive wells and actions to permanently terminate operations, such as dismantling pipelines, buildings and reclamation of the contract area, as well as decommissioning and obligations to prevent environmental pollution at the production site.
The Company calculates asset retirement obligations separately for each contract. The amount of the liability is the present value of the estimated costs that are expected to be required to settle the liability, adjusted for the expected inflation rate and discounted using average long‑term risk‑free interest rates on government debt of transition economies, adjusted for risks inherent in the Kazakhstan market.
As of 31 December 2023, the carrying amount of the Company’s provision for liabilities to liquidate oil and gas assets was KZT 124 bln (as of 31 December 2022: KZT 88 bln) (for details, see Note 30 in the consolidated financial statements).
Oil and gas trunklines
In accordance with the Law of the Republic of Kazakhstan On Trunk Pipeline, which entered into force on 4 July 2012, KMG’s subsidiary KazTransOil has a legal obligation to liquidate the trunkline after the end of operation and implement subsequent measures to restore the environment, including land reclamation. The provision for the obligation to abandon pipelines and land reclamation is estimated based on the cost of dismantling and reclamation works calculated by KMG. As of 31 December 2023, the carrying amount of KMG Group’s provision for the obligation to abandon pipelines and reclaim land of the Company amounted to KZT 46 bln (as of 31 December 2022: KZT 41 bln) (for details, see Note 30 in the consolidated financial statements).
Environmental remediation
KMG also makes estimates and makes judgements on creating provisions for obligations for environmental clean‑up and rehabilitation. Environmental costs are capitalised as an expense based on or attributable to their future economic benefits.
The Company’s environmental remediation provision represents management’s best estimates based on an independent assessment of the expected costs required for KMG Group to comply with the existing Kazakh and European regulatory frameworks. As of 31 December 2023, the carrying amount of the provision for environmental liabilities was KZT 39 bln (as of 31 December 2022: KZT 681 bln) (for details, see Note 36 in the consolidated financial statements).
Water is an integral part of all KMG production processes. KMG adheres to the principles of the UN Global Compact and integrates the Sustainable Development Goals (SDGs) into its operations. The Company adheres to all 17 SDGs, including Goal 6, Clean Water and Sanitation. In its activities, the Company strives to reduce water consumption, increase water use efficiency, drive up water reuse and recycling, improve the quality of effluents, and minimise the impact on natural water bodies.
KMG is a vertically integrated company engaged in the production, transportation, and processing of hydrocarbons. All processes consume a lot of water. KMG takes water from surface and underground sources, municipal water supply systems, and the Caspian Sea. Wastewater from KMG’s operations mainly goes to specialised receivers: storage ponds, and evaporation and filtration fields. Those facilities are technical structures designed for natural treatment of wastewater and preventing environmental pollution. Operations that do not have their own storage facilities transfer wastewater to dedicated companies for treatment and disposal. The quality standards for discharged water established by environmental laws are met through the use of mechanical and biological methods of effluent treatment. However, no wastewater is discharged into surface natural water bodies.
One of the Company’s most important objectives is to increase the reuse of treated effluents by returning them to the process, using them for irrigation of green areas, and dust suppression on construction sites and roads.
KMG uses the World Resources Institute’s (WRI) Aqueduct water stress tool to map operated assets in water stressed areas. For such regions, KMG develops water management measures to use less fresh water, increase recycled water, and closely monitor water use.
To prevent water shortage risks, ensure the planned economic growth, and improve the water management system, KMG Group has developed a Water Resources Management Programme, which is expected to be approved in 2024.
Atyrau Refinery
The Tazalyq project is one of the key ongoing environmental initiatives of Atyrau Refinery. It includes the upgrade of the evaporation fields, mechanical treatment plants, and biological treatment facilities, as well as the construction of an advanced treatment facility. The project will have a significant environmental effect by improving the quality of wastewater treatment and eliminating harmful evaporation into the atmosphere from open tanks of the treatment plant and environmental impacts from evaporation fields.
This project will help double the capacity of mechanical treatment plants. In addition, a pipeline from Atyrau Refinery to the municipal sewage treatment facilities was installed in place of the existing open channel, which was used to discharge wastewater from Atyrau Refinery to its evaporation fields, thus eliminating the release of hazardous substances into the environment. The reclamation of Atyrau Refinery’s evaporation fields is also underway. It consists of several stages: drainage of evaporation fields, mowing of reeds, deep ploughing, treatment with a biological agent, and triple reclamation.
Astrakhan–Mangyshlak main water line
2023 saw the launch of the Astrakhan–Mangyshlak main water line in the Atyrau Region after its expansion as a result of comprehensive reconstruction. The water pipeline was upgraded one year ahead of schedule.
Following the upgrade, the water line will become a source of additional 60 thous. m3 of water for the population, businesses, and agricultural facilities of the Atyrau and Mangistau regions.
As part of the project, the worn‑out equipment was modernised and two sections of the main water pipeline with a total length of about 177 km were replaced. With a workforce of over 500 people involved in the construction, the project successfully increased the pipeline’s daily throughput capacity from 110 thous. m3 to 170 thous. m3.
A desalination plant with a daily capacity of 50 thous. m3 is currently under construction in Kenderly. A 105 km long main water pipeline will be built from Kenderly to Zhanaozen.
In addition, the Caspi water supply plant is being reconstructed to double its capacity to 40 thous. m3.
Construction of desalination plants near the Kenderly recreational area, Mangistau Region
KMG is building a seawater desalination plant with a capacity of 50 thous. m3 per day next to the Kenderly recreational area. This project will solve the problem of drinking water shortage for the residents of Zhanaozen, while also having a multiplier effect on the development of tourism, business, and agriculture. The construction is scheduled to be completed by the end of 2024, with the plant reaching its design capacity in the spring of 2025.
Karazhanbasmunai
KBM’s Karazhanbas field in the Mangistau Region launched a formation water desalination plant to address the issue of water supply to the field. Once the full capacity is reached, the formation water processing will amount to 42.5 thous. m3 per day, while desalinated water production will reach 17.0 thous. m3 per day, thus releasing a significant volume of water for the needs of the region’s population.
Since 2020, the Company has been calculating its water footprint and making water management disclosures on the Carbon Disclosure Project (CDP) platform as part of the Water Security Questionnaire. The information for 2022 is published on the CDP website.
KMG and its subsidiaries and associates prioritise the life and health of employees over the results of production activities and put a special emphasis on the elimination of hazardous production factors in occupational health and safety.
KMG’s Occupational Health and Safety Policy seeks to engage every employee in building a robust safety culture. Management teams at KMG and its subsidiaries and associates take a zero tolerance approach to losses and damage caused by accidents (including traffic accidents), emergencies, as well as by the use of alcohol, narcotic drugs, psychotropic substances or their analogues. KMG is committed to ensuring compliance with both national laws and relevant international and national standards. The Company will continue to work to ensure a high level of production safety in accordance with global standards and best practices.
2023 highlights
As one of the industry leaders in the Republic of Kazakhstan, KMG places a strong emphasis on health and safety of its employees and local communities across its footprint. According to our employees, the Company creates safe working conditions and complies with the highest standards to ensure health and safety at the workplace.
The number of injuries associated with workplace accidents decreased by 19% year‑on‑year (from 36 injuries in 2022 to 29 in 2023).
The number of road accidents dropped by 21% (from 24 in 2022 to 19 in 2023), while the number of fires fell by 100% (from 1 in 2022 to 0 in 2023).
In 2023, despite the positive performance in the realm of accident prevention, there were two fatal accidents related to labour activities (one employee of PetroKazakhstan Oil Products was killed in a road accident and one employee of Ken‑Kurylys‑Service died as a result of impact of moving objects).
Process safety management
As part of the efforts to prevent accidents and incidents in 2023, subsidiaries and associates were consulted and advised on how to organise and ensure process safety / manage barriers. Also in 2023, 23 scheduled audits were carried out on the industrial safety of subsidiaries and associates. The auditors issued 220 items of recommendations to improve the industrial safety at hazardous production facilities of KMG Group.
As part of rolling out KMG’s corporate Rules for Isolation of Energy Sources, the subsidiaries and associates were provided with explanations on the implementation of the LOTO industrial safety system. The implementation and application of LOTO is monitored by KMG’s Health, Safety, and Environment Department. In 2024, we plan to continue introducing and using the LOTO system in the production operations of KMG Group.
Besides, in order to consistently improve industrial safety at the facilities of KMG’s subsidiaries and associates, an emergency drill was conducted to eliminate a blowout and a fire at a well and rescue a victim at the training grounds of PD Zhetybaimunaigaz (MMG), with the participation of a unit of the Mangistau branch of the Centralised Republican Headquarters of Militarised Professional Emergency Services and the Semser Ort‑Sondirushi private fire‑fighting service. The event was attended by observers from Samruk‑Kazyna, KMG, Department of the Industrial Safety Committee, Department of Emergency Situations in the Mangistau Region, and KMG’s subsidiaries and associates. The drill participants practised cooling of the well equipment, reduction in the intensity of heat radiation from the blowout, determination of the gas contamination zone, and sealing of the wellhead and killing of the well by injecting heavily weighted drilling mud.
Transport safety
When considering road accident statistics, it is worth noting that there are objective factors that contribute to the risk of incidents. One such factor is a large number of vehicles (more than 11,000 across the Company) and the very nature of service companies’ operations – the need to travel regardless of the time of day, season, and weather conditions. The second factor is the geography of the Company’s subsidiaries scattered across the Republic of Kazakhstan, as well as their location in big cities and towns where there is a high risk of road accidents due to the fault of a third party. For example, 15 of 19 road accidents (79%) that occurred in 2023 were caused by third parties.
As part of ensuring transport safety, protecting the life and health of people in the process of operating and maintaining motor vehicles, preventing road accidents, and reducing exposure of the Company’s employees to potential risks of injury, we make consistent efforts to improve the level of transport safety:
- In 2023, 1,905 employees of subsidiaries and associates (1,451 employees of KMG’s subsidiaries and associates and 454 employees of contractors) completed a defensive driving training in line with international RoSPA standards.
- In order to raise awareness among KMG Group employees about the need to use seat belts and reduce the number of injuries in road accidents, the Company undertook practical demonstration of the Convincer frontal collision simulator, which was attended by 7,783 employees of KMG’s subsidiaries and associates.
- As part of the Travel Management project to implement an automated vehicle monitoring system, in 2023 diagnostics of transportation management processes were completed at KBM, OMG, MMG, OTC, OSC, and KTO (roadmaps for the project implementation were approved at KBM, OMG, OTC, and OSC).
Fire safety
No fires occurred at KMG’s facilities in 2023. However, the following fire safety issues were registered:
11 ignitions (Atyrau Refinery (2), OMG (2), OMS, MMG, Petromidia Refinery (2), EMG, KGM, OSC), 1 flash (OMG), and 3 smoulderings (KTO, Atyrau Refinery, MMG).
According to the applicable laws, “fire”, “ignition”, “smouldering”, and “flash” have different attributes and definitions. Thus, none of the above cases was included in the fire statistics.
On 21 June 2023, a mild hydrocracker (MHC) ignited at Petromidia Refinery in Romania following special maintenance. No injuries were reported. All employees of the unit and other sections of the refinery were evacuated.
To strengthen compliance with fire safety requirements, KMG developed and approved the Integrated Fire Safety Action Plan for 2022–2024, providing for short‑, medium‑, and long‑term measures as well as preventive initiatives.
The reporting year saw scheduled fire drills held in all subsidiaries and associates in accordance with the Integrated Plan and in line with the instructions of Samruk‑Kazyna.
In July 2023, drills were held at MMG with the participation of Samruk‑Kazyna and Kazakhstan’s Ministry of Emergency Situations.
On 20 September 2023, fire drills were held to eliminate a fire at the tank farm of Caspi Bitum with the participation of the Minister of Emergency Situations of the Republic of Kazakhstan.
In 2023, KMG Corporate Centre conducted two fire drills involving people evacuation and extinguishing of a simulated fire in the building.
HSE interaction with contractors
The Company seeks to improve the processes of HSE interaction with contractors on the basis of identification, assessment, and mitigation of risks at all stages of work and services provided by contractors and subcontractors at KMG Group’s production facilities.
The Company requires contractors to observe and fulfil the legislative requirements of the Republic of Kazakhstan, KMG Life‑Saving Rules, and the Company’s HSE policies and standards.
In order to reduce incidents involving contractors, during 2023 KMG’s HSE Department conducted compliance audits in 12 subsidiaries and associates to assess their HSE interaction with contractors. The audit yielded 587 performance improvement recommendations.
Based on the analysis of organisational structures of HSE functions across the Group in 2023, subsidiaries and associates received a recommendation to employ a relationship manager for HSE contractors.
Agreements with contractors will also provide for fines to contractors in breach of statutory requirements and KMG’s HSE standards.
To manage potential hazards and prevent HSE incidents, the Company put in place Life‑Saving Rules applicable to contractors. These rules inform employees of actions they can take to protect themselves and their colleagues from accidents. In accordance with the Policy and management system standards, KMG Group employees and contractors are entitled to reject or suspend work in case of a situation reasonably believed to be potentially threatening to health, safety or environment.
As a way to improve communication and efficiency of HSE interaction with contractors, a forum was held for the heads of HSE services at subsidiaries and associates to discuss the effectiveness of contractors’ accident investigation and HSE management procedures. The event was attended by Samruk‑Kazyna officials. The forum focused on the most relevant cases of process approaches and HSE management of contractors, in particular, the analytical approach to solving problems in process management based on the Deming PDCA cycle and its application to the management of contractors based on the example of Chevron.
The Company’s key HSE requirement is pre‑mobilisation audit for compliance of the contractor’s machinery, equipment and personnel prior to the commencement of work, appointment of HSE officers from among the contractor’s key employees, holding a kick‑off meeting with the contractor, development and implementation of the contractor’s HSE Plan (prior to the commencement of work, during work, and upon completion) and evaluation of the contractor’s HSE performance.
Digitisation of HSE processes
2022 saw the completion of a pilot project to implement an automated vehicle monitoring system. The Travel Management project was implemented to improve transport safety, foster a safe driving culture, and establish a single centralised digital platform.
Given the positive effect on transport safety as a result of the Travel Management system introduction at EMG, as part of the phased replication of the project to other KMG subsidiaries and associates, in 2023 diagnostics of transportation management processes were completed at KBM, OMG, MMG, OTC, OSC, and KTO, and roadmaps for project implementation were approved.
As part of the industrial safety processes digitisation, EMG continues the implementation of electronic work permits system. Starting December 2023, the system has been put into operation for all EMG’ production units. In 2024, the Company was developing TUMAR, an automated intelligent industrial safety system for preventing incidents and reducing the negative impact on employees when carrying out hazardous operations and during underground workover.
Improving the HSE management system
In 2018, KMG decided to join the International Association of Oil and Gas Producers (IOGP) as a full member.
Over the years of its membership in IOGP, KMG has learnt and applied IOGP best global practices and recommendations, which has had a positive effect on KMG’s performance and overall HSE management system, as well as KMG’s capabilities and rating on the international scale.
Since 1991, IOGP has analysed 2 thous. fatal accidents at some 100 IOGP member companies and identified the most frequent safety violations.
To prevent these violations, nine vital Life‑Saving Rules have been drafted to inform workers of actions they can take to protect themselves and their colleagues from from situations with negative implications.
As part of its membership in the Association, KMG has developed and implemented the KMG Life‑Saving Rules at its subsidiaries and associates, which carried out campaigns to raise employee awareness of the Rules by means of video materials and presentations. A message was circulated on behalf of the Chairman of KMG’s Management Board on the importance of the KMG Life‑Saving Rules and the right to refuse to carry out any work if it is unsafe.
In order to promote a safety culture among employees and according to Samruk‑Kazyna’s Occupational Safety Action Plan, some 30 thous. employees of KMG and its subsidiaries and associates took training in safety culture.
The Company manages occupational health and hygiene matters in accordance with Kazakh laws and international occupational health standards. KMG is strongly focused on employee health protection and improvement, irrespective of the specific production process involved.
In 2023, the number of non‑work related fatalities among employees of subsidiaries and associates reduced by two incidents, or 20%, year‑on‑year, the main reason behind these fatalities being cardiovascular diseases.
As part of strategic initiative 24 Personnel Health Management under the KMG Development Strategy for 2022–2031, the Company developed and approved:
- Employee Health Management Action Plan for 2023–2025;
- Corporate Standard on Mandatory Medical Examinations;
- KMG Group’s Regulations on Emergency Medical Care as amended;
- Regulations on Drafting a Group‑wide Standard Programme of Occupational Hygiene.
According to the Regulations on Emergency Medical Care, KMG Group conducts annual and regular medical drills to test the Emergency Medical Response Action Plan at each production facility. In 2023, subsidiaries and associates had over 560 medical drills, including those invovling contractors deployed at production sites. The drills covered the following topics: first aid in case of falling from a height, loss of consciousness, poisoning, cardiac arrest, etc.
The Company continues the implementation of hardware systems for medical examinations and rolled out 44 such systems at KMG’s subsidiaries and associates by the end of 2023.
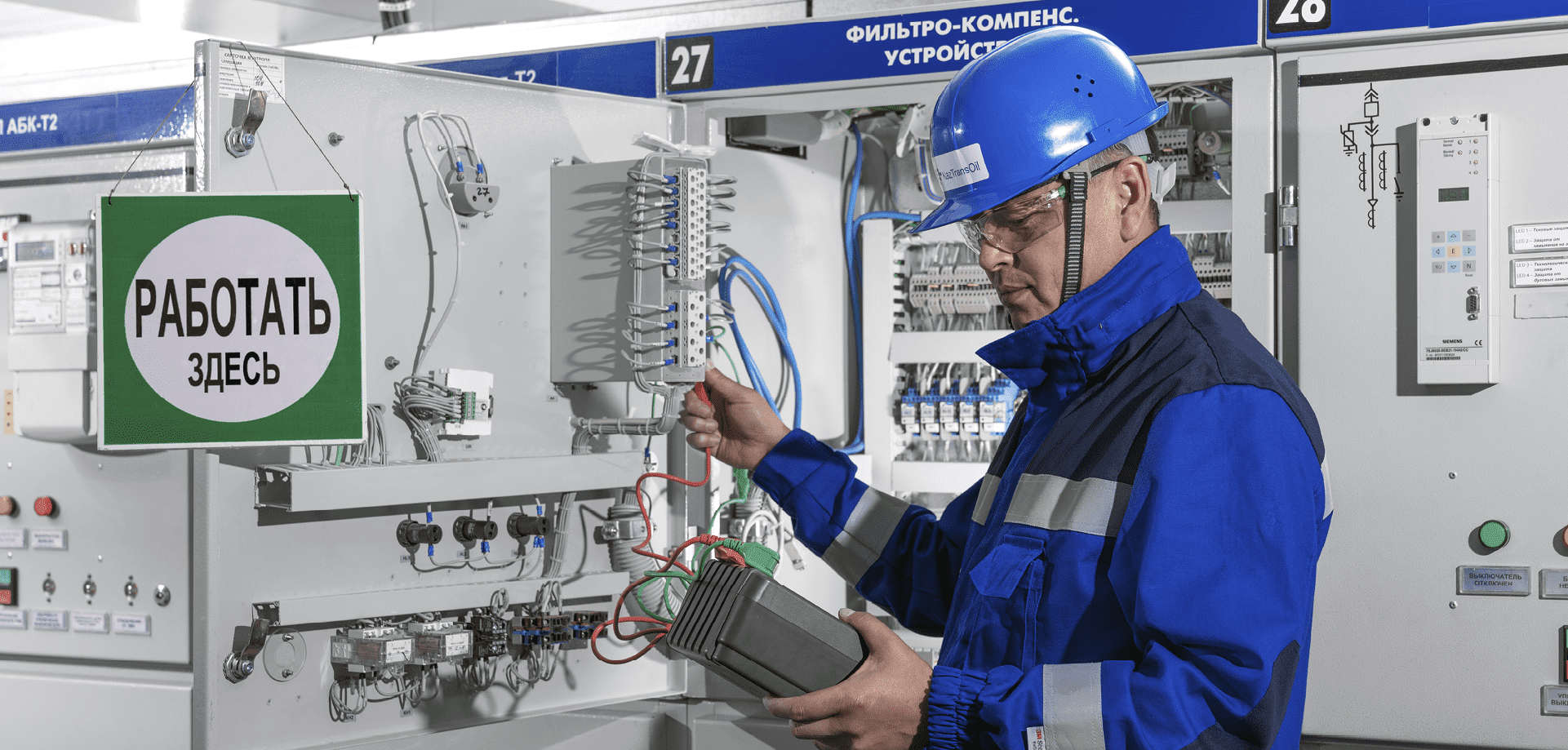