Petrochemicals

KMG will be strongly involved in developing Kazakhstan’s petrochemical industry with support from the government, which is expected to significantly boost the national economy as growth in the petrochemical sector will have a multiplier effect on the entire domestic market.
Key objectives of KMG’s petrochemical projects:
- build the first gas chemical complex and establish a petrochemical cluster in the Republic of Kazakhstan;
- use the available large volumes of gas for the petrochemical complex;
- manufacture export‑oriented products with high added value;
- produce polymers to diversify industry sectors.
Polypropylene
About KPI Inc.
Kazakhstan Petrochemical Industries Inc. Limited Liability Partnership (KPI Inc.) is the operator of Phase I of the first integrated gas chemical complex project in the Atyrau Region. Established in 2008, the Partnership has the abbreviated name KPI Inc.
Project participants: National Company KazMunayGas with 49.5%; SIBUR Holding with 40%, Samruk‑Kazyna Ondeu with 9.5% (the sole member of Samruk‑Kazyna Ondeu is Sovereign Wealth Fund Samruk‑Kazyna. Samruk‑Kazyna Ondeu was established to carry out the commission of the President of the Republic of Kazakhstan to implement projects in the chemical industry); Firm Almex Plus with 1% (a private investor, member of a major Kazakhstani holding group, Holding Group ALMEX).
KPI Inc. polypropylene production was officially launched in November 2022 as part of Phase I of the integrated gas chemical complex construction project in the Atyrau Region. Polypropylene is used as feedstock in mechanical engineering, medicine and electrical engineering, production of packaging materials, containers, fibre, pipes and fittings for hot water supply, office equipment, consumer electronics, consumer goods, outdoor and office furniture.
Plant highlights
A capacity of 500 thous. tonnes of polypropylene per year represents:
- about 1% of global polypropylene production;
- 26.3% of total polypropylene production in the Russian Federation;
- more than total polypropylene production in Turkmenistan, Uzbekistan, and Azerbaijan.
Feedstock: propane from the Tengiz field, free of harmful impurities, thus minimising the environmental impact.
Technologies used: Catofin (propane dehydrogenation) and Novolen (propylene polymerisation) technologies by Lummus Technology Inc. (USA).
- Similar complexes have been built in five countries (Saudi Arabia, USA, Belgium, South Korea, and China).
- 77% of equipment was manufactured in Europe, the USA, South Korea, Japan, and India.
Project cost: total project cost – USD 2,630 mln, including EPC contract – USD 1,865 mln.
Funding: USD 2 bln (loan from China Development Bank, PRC).
New jobs:
- during construction (temporary) – over 4,000;
- during operation (permanent) – 630.
General contractor: China National Chemical Engineering Co. (CNCEC, PRC).
Effect of the project:
- covering Kazakhstan’s domestic demand (import substitution) for polypropylene (Kazakhstan market capacity is about 50 thous. tonnes per year);
- opportunities for SMEs to make higher value‑added products from polypropylene for the construction, medical, automotive, food processing, textile industries, etc.;
- new jobs in SMEs and related industries;
- the contribution to the country’s GDP will be up to 1%.
Current status
Currently, work is underway to bring the entire complex to a stable operating mode. Construction and installation have been completed, and off‑site facilities, propane loading rack and propane storage park have been put into operation. Commissioning works are underway. Given the scale and complexity of production processes and the products, and the fact that this is Kazakhstan’s first petrochemical plant, coupled with the industry’s specific requirements, it takes a long time to achieve stable production across the entire complex.
2023 results
Today, KPI Inc. produces six polypropylene grades in accordance with its grade range offering (with the total of nine grades based on the grade range and 64 grades based on the project design):
- РР Н270 FF (1105 RC)
- PP H350 FF (1105 SC)
- PP H120 GP (1100N)
- PP H030 GP (1100K)
- PP H031 BF (1104K)
- PP H036 BF (1104K)
Production of the remaining three polypropylene grades is expected to be set up in January 2024.
Another highlight of this year was the launch of production of phthalate‑free polypropylene grades (used to produce more environmentally friendly end products).
KPI Inc. has also developed its Production Stabilisation Programme for 2024 to achieve maximum performance based on the Uptime indicator allowing to detect production losses and find ways to eliminate them for a systematic and effective loss identification.
To quickly train the production team, a Standard Operating Procedure (SOP) has been introduced offering step‑by‑step instructions for young specialists.
Over the reporting year, some 50 Kazakh manufacturers have already switched to KPI Inc. polypropylene praising its quality. It is fair to say that KPI Inc. has started to fully cover domestic demand in polypropylene.
2023 events
- On 22 October 2023, a full power outage occurred with no power supplied from KUS’ steam and gas turbine power plant resulting in a technological failure at the Complex and emergency shutdown of the propane dehydrogenation and polypropylene production operations. This incident will impact the timing of warranty testing and commissioning of the Complex facilities.
- Commissioning certificate will be signed after the completion of full adjustment and test running of the equipment at designed capacity, Licensor inspection, completion of operational and warranty tests, as well as the completion of claim settlement procedures involving CNCEC.
- Commissioning a petrochemical complex takes some time given the complexity of the production processes and the fact that this is Kazakhstan’s first project of its kind.
Expected deliverables
- creation of a petrochemical cluster in the Republic of Kazakhstan for the production of petrochemical products using feedstock from the Tengiz field;
- manufacture of export‑oriented products with high added value;
- production of polymers to diversify national industry sectors;
- headcount at KPI Inc. totals 628 employees.
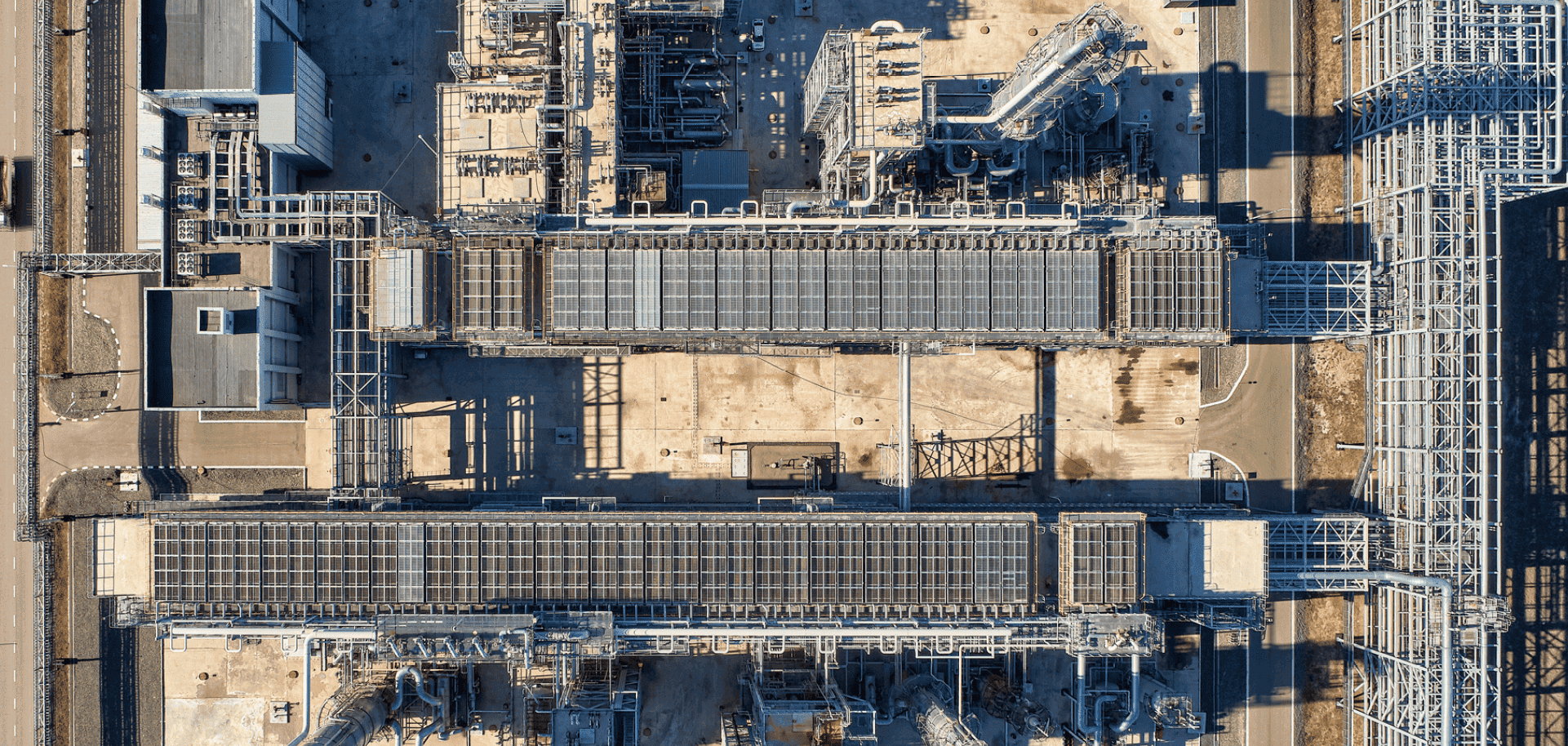
Tengizchevroil ships feedstock gas by rail to a plant located 40 km away from the regional centre.
Propane (C₃H₈) comes from Tengiz already purified from harmful substances. Each of the eight 145‑tonne reactors of South Korean Wooyang HC (the heart of the plant) converts (dehydrogenates) propane into propylene (C₃H₆) with the release of hydrogen.
Polypropylene (C₃H₆)n is produced by polymerisation at a Lummus Technology (USA) plant, there being only six such plants in the world.
Environmental safety
The production process is associated with minimal water consumption: 82% of the liquid used is returned to the production cycle, which partially compensates for the energy costs of endothermic operations. As a consequence, there are no emissions to vaporisation fields. In other words, the production is as environmentally friendly as it can be.
Polyethylene
As part of Phase II of the integrated petrochemical complex construction, on 7 November 2022 KMG and SIBUR signed binding documents for joining the Polyethylene (PE) project. The move was in line with KMG’s strategy to join forces with a strategic partner which is among Top 5 polymer companies in the world and has a strong track record of successfully delivering large‑scale projects. The project’s annual design capacity is 1,250,000 tonnes of polyethylene. The project is expected to be completed in 2028.
It will be required to supply feedstock (ethane) to the PE project. To this end, negotiations are ongoing with Tengizchevroil to consider building a gas separation unit with a capacity of 9.7 bln m3 (the GSU) to create infrastructure for extracting ethane from dry gas. Preferential government funding for the GSU is also being worked out.
The PE project is implemented as part of the National Project “Sustainable economic growth aimed at improving the welfare of Kazakhstanis”, and meets KMG’s long‑term strategic goals, which include improvement of the value chain efficiency, business diversification and expansion of the hydrocarbon product portfolio.
One of the main objectives for KMG and the entire oil and gas industry in Kazakhstan is the processing and commercialisation of re‑injected associated gas, especially at the major oil and gas projects (Tengiz, Kashagan and Karachaganak). A number of projects in this field are underway in Kazakhstan, including the processing of propane (polypropylene production), ethane (polyethylene production) and butane (butadiene production) from the Tengiz field, as well as construction of gas processing facilities at the Kashagan field.
In addition to its advantageous location close to the feedstock production facility, the key competitive advantages of the PE project include:
- high ethane fraction content (up to 14%) in the feedstock;
- attractive cost of feedstock;
- lower infrastructure costs, as they are split among several projects;
- advantageous location and access to main markets;
- accumulated KMG experience and expertise in implementing large‑scale projects of refining facilities upgrade and construction.
Polyethylene and ethylene copolymers serve as the basis for a wide range of products widely used in the national economy: sewer, water and gas pipes, fittings, films of all grades (food, packaging, bags, etc.), fibres, non‑woven materials, monofilaments, film threads, electrical insulation, shells for boats and cross‑country vehicles, technical equipment parts, containers (bottles, crates, jerrycans, etc.), technical, household and medical items, for the manufacture of various containers of large and small size, pallets, crates, etc.
Granulated polyethylene is a non‑hazardous non‑toxic product. It does not produce toxic emissions at room temperature and is not harmful to human health if in contact with skin. No special precautions are required for working with it. However, small polymer dust when breathed in and entering the lungs can cause sluggish fibrotic changes in the lungs. Due to its low conductivity, polyethylene can generate static electric charges.
When in a stable state, polyethylene is not harmful to the environment as it does not form toxic compounds at ambient temperature when exposed to atmosphere or wastewater where other substances or factors are present. Polyethylene and the additives it contains are known to cause no damage to the ozone layer.
The Company plans to supply finished products to both domestic and international markets. The capacity of Kazakhstan’s domestic market is estimated at about 180,000 tonnes of polyethylene per year, with an expected annual growth rate of 4% on average. Target export markets include the CIS, China, Turkey, and Europe, where the consumption of polyethylene, including imported one, is also expected to go up. Located at the crossroads of transport corridors connecting Asia and Europe, Kazakhstan has a favourable trade, economic, and strategic position.
Engineering design
Today, the Project is in the active design stage:
- feasibility study developed with a positive opinion received from the government regulator Gosexpertiza (Independent State Expert Review) on 24 November 2023;
- EBD/FEED and design and estimate documentation are being developed.
The main purpose of the current Design Phase is to prepare for the Final Investment Decision (FID) to be made by the Project participants and to move to the Implementation Phase. The current phase includes an assessment of the implementation and subsequent operation risks and opportunities, including in terms of future profitability. Project FID is expected in 2024.
Economic attractiveness of the project
In case of a positive FID, the PE project will improve the efficiency and diversification of the Company’s business, as well as the competitiveness of the country’s economy as a whole due to the production of advanced and high‑margin products.
The PE project has significant social and economic benefits for the country as it will help maintain social stability in the region and create new jobs. In particular, about 8,000 jobs will be created during the construction and about 800 permanent jobs – during the operation.
Indicative cost of the Project is USD 7.7 bln.
The pattern of the PE project financing is under development and involves a combination of borrowings and the Company’s own funds.
Strategic partners
On 28 March 2023, SIBUR Holding was officially registered by Kazakhstan’s authorities as a 40% stakeholder in joint venture Silleno LLP.
On 16–17 October 2023, binding documents regarding Sinopec’s entry into the project were signed at the Belt and Road Forum for International Cooperation in Beijing. The legal formalities surrounding its entry into the project are expected to be completed in Q1 2024 upon receipt of domestic approvals in China.
By the end of 2023 the Project’s ownership structure: KMG with a 49.9% stake, SIBUR with 40%, and KMG PetroChem with 10.1%. Target ownership structure: KMG to hold 29.9%, SIBUR and Sinopec each to hold 30%, and KMG PetroChem to hold 10.1%.
Reporting period achievements
- March 2023: SIBUR’s entry into the Project finalised;
- April 2023: EBD/FEED development contracts signed;
- October 2023: binding documents on Sinopec’s entry into the Project signed;
- November 2023: Process Design Packages (PDP) received in full from Licensors CPChem, Axxens and Univation;
- November 2023: Project’s feasibility study approved by Gosexpertiza;
- December 2023: contract signed with the Kazakh Institute of Oil and Gas for the development of design and estimate documentation;
- December 2023: Bank of China engaged as a financial advisor to raise capital.
Other petrochemical projects
Construction of a terephthalic acid and polyethylene terephthalate (TPA/PET) plant, and Urea projects are currently at the preFS stages, specifically:
- in the TPA/PET project, preliminary planning efforts have been taken to supply the Project with feedstock and infrastructure with marketing report developed, and preFS development launched;
- in the Urea project, work is underway to determine feedstock sources and engage a strategic partner with the preliminary process flow diagram reviewed and potential licensors determined.
PreFS results for the projects are expected in Q4 2024.
For reference: indicative annual capacity of the TPA/PET project comprises up to 735 thous. tonnes of polyethylene terephthalate. The Project is scheduled for completion in 2029. Indicative annual capacity of the Urea project comprises up to 1.15 mln tonnes of urea. The project is scheduled for completion in 2028.
As resolved by Samruk‑Kazyna, the Butadiene project has been transferred to the Fund with Butadiene LLP re‑registered on 19 June 2023.
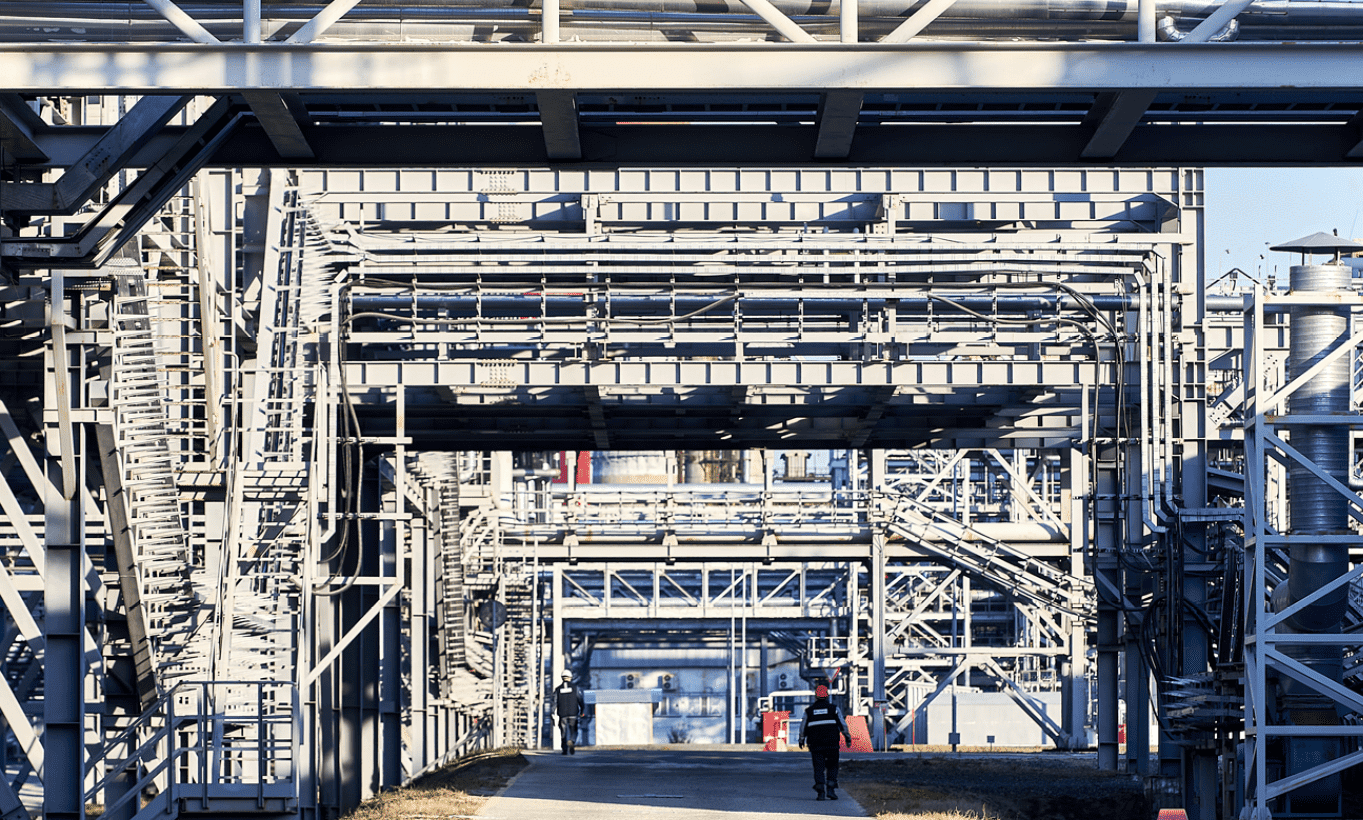