Innovative technology development
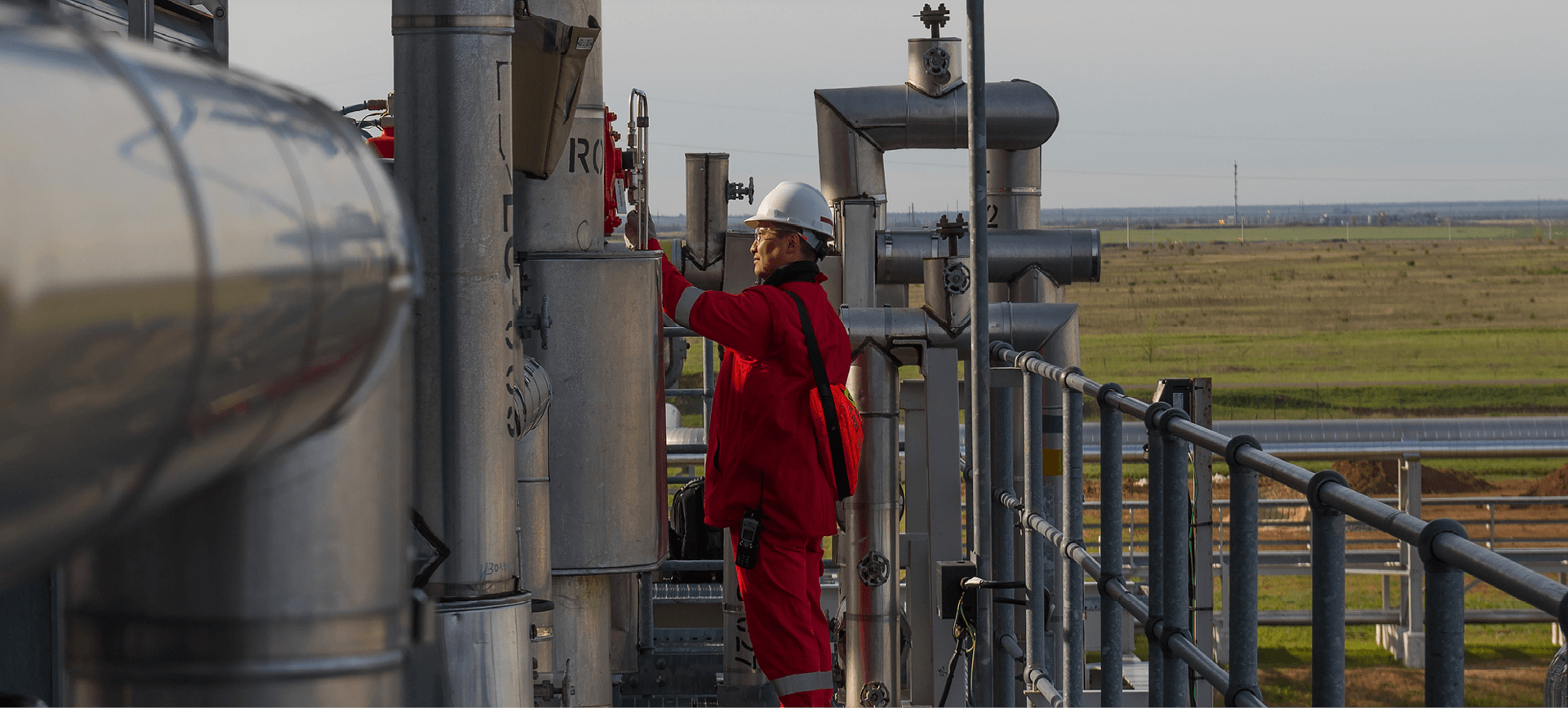
KMG Engineering
KMG Engineering was founded in 2014 to provide comprehensive scientific and engineering support for exploration, production, and drilling of KMG’s hydrocarbon resources.
KMG Engineering has its head office in Astana and two branches: Atyrau Branch LLP in Atyrau and KazNIPImunaygas LLP in Aktau, which provide direct real‑time support for KMG’s assets.
Strategic objectives of KMG Engineering and its branches
- R&D advancement and new technology implementation to develop resource base;
- R&D support for reliable and efficient field operation;
- implementing advanced technologies as part of production digitalisation;
- developing hydrogen energy projects and competencies.
To deliver against its strategic goals, KMG Engineering focuses on addressing end‑to‑end objectives in the areas of technology development, digitalisation, business process optimisation, IT, HR, and risk management.
Exploration
In 2023, for the first time in its history, KMG conducted pilot seismic operations using unique arrangement of field equipment to study the subsurface geology of the Caspian sedimentary basin, covering depths of up to 20 km. In 2024, the Company plans to test wireless sensors in seismic surveying to streamline timelines and survey areas. Also in 2024, it is planned to test pulse source technology for seismic surveying in environmentally sensitive areas of the Caspian Sea to minimise an environmental impact.
Based on the analysis of geological and geophysical data, five new promising blocks were identified for exploration in the medium and long run – Bozashi, South Kalamkas, South Kamyshitovy, Zhylyoi, and Kairan – Aktoty – Tazhigali Subsalt. KMG Engineering also revised project seismic profiles and measured investments in seismic work at three underexplored basins.
The geological survey of the areas of geological exploration has been completed, and the processing of seismic data for the Kalamkas‑Sea and Hazar deposits continues. A dynamic analysis of 3D seismic data was done for certain areas, and R&D assistance was provided in well drilling and testing.
The company drafted reports on reserves reestimation, increase and conversion, and approved design documents for constructing a 5,500 m deep exploration well in the Turgai Paleozoic block. A hydrocarbon exploration project at Karaton Subsalt was approved, while those for the Taisoigan‑1 and Taisoigan‑2 blocks are at the development stage.
Well drilling and workover
KMG Engineering’s Online Drilling Competence Centre focuses on real‑time drilling control and support as key to stable field production. Drilling of new wells, including horizontal ones, is one of the main ways to sustain oil production at the mature fields of KMG’s subsidiaries and associates. This helps reduce the total number of wells, make oil recovery more efficient and tap into new reservoirs, including those with high‑viscosity oil.
In 2023, Embamunaigas drilled 16 horizontal wells, with the average reservoir penetration of 86%, which proves the applied techniques and solutions as highly efficient. To streamline drilling, 1D geomechanical models were built and updated to gain a deeper insight into the geological structure and select the best drilling parameters.
Cementing quality is important to ensure the reliability of well production strings. In 2023, cementing strength of completed wells at KMG’s subsidiaries and associates improved to reach 78.53%. This was possible thanks to continuous analysis and enhancement of relevant technologies, which reduces the risk of incidents during well operation.
Along with drilling new wells, it is vital to conduct overhauls to secure proper well operation in the long run. Efficiency of all types of overhaul is subject to continuous monitoring in order to streamline processes and introduce cutting‑edge technologies.
The Company places a special emphasis on the use of cutting‑edge technologies and design of new techniques. For example, Radiagreen EME Salt lubricant for drilling fluids and Welltec Light Packer (metal hydraulic expandable packers) serve to make drilling more efficient and construct reliably sealed wells.
Over the last 11 months of 2023, our facilities actively introduced advanced drilling and overhaul solutions, which increased the productivity and efficiency of our operations. After switching to a new BIT 215,9 VT 513 drill bit, the drilling speed has been accelerated by 43.72% and reduced work completion time, improving overall project performance at Zhetybai and Asar fields. Capital and routine well repairs completed, modern lifting equipment and machinery introduced, enhancing reliability and safety of production processes. These results are driven by our ambition to innovate and apply modern solutions.
In 2024, a LED display is planned to be installed to monitor drilling and introduce Petrel and StarSteer geosteering software to cover as much of the target reservoir as possible. Landmark, Techlog and Peloton software will serve to provide technological support aimed at accident‑free drilling and cutting down idle time.
All in all, these measures and technologies seek to make oil production more efficient and ensure sustainable field development in the long run.
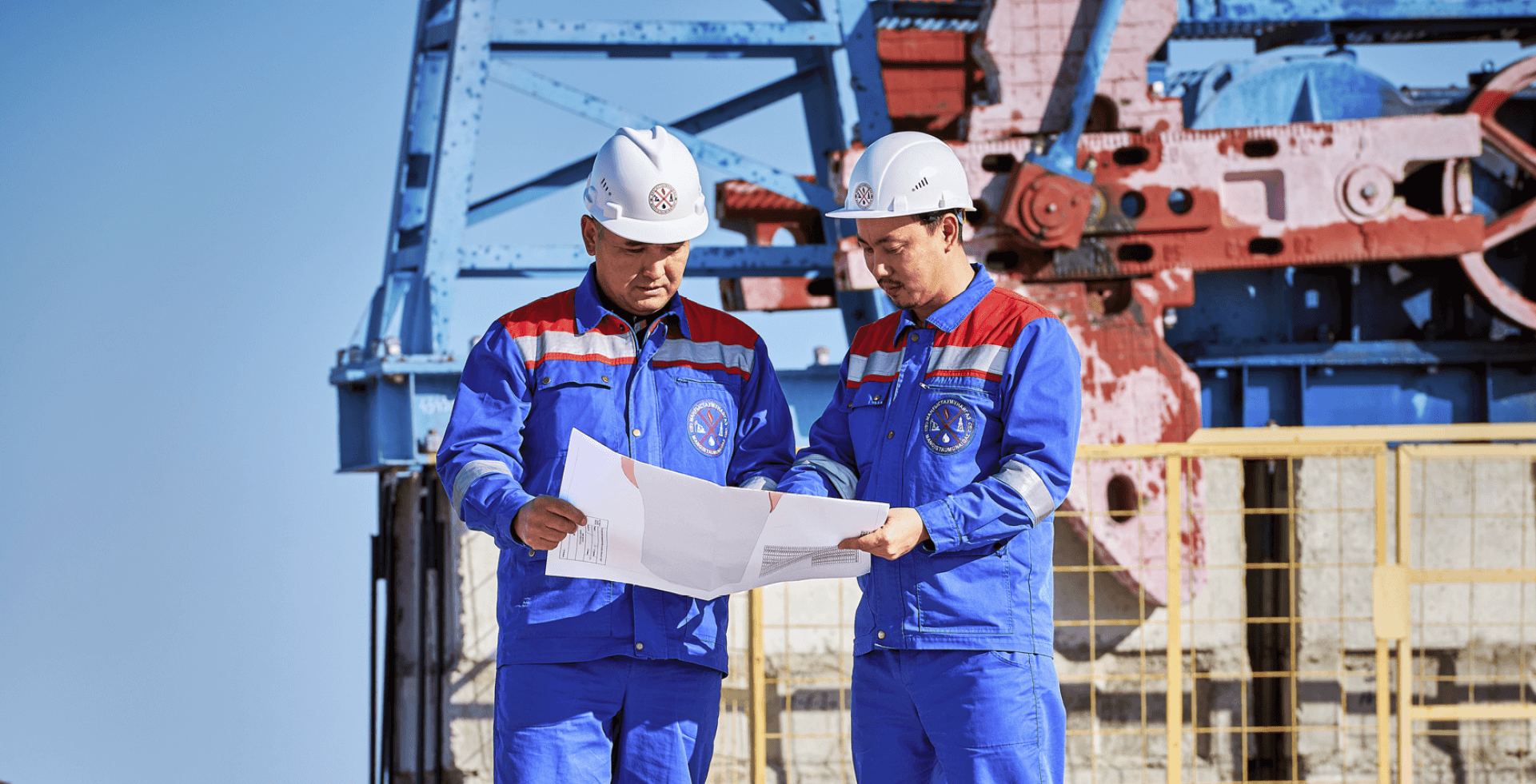
Production
To ensure stable production levels at its assets, the Company focuses on slowing down the decline of basic production and intensifies rational recovery of residual hydrocarbon reserves. KMG Engineering provides continuous R&D support to drilling, production and refining processes. The key strategies to maintain basic production include boosting performance and reducing the number of inefficient wells. The achievement of these objectives include the analysis of the effectiveness of methods to enhance oil recovery, the identification causes of failure, the development of corrective actions, and improvement of the efficiency of inefficient wells.
To keep geological and hydrodynamic models up‑to‑date, we created and updated them considering several development scenarios for Kalamkas, Karamandybas, Alibekmola and Kozhasai fields. Sector geological and hydrodynamic models were put in place to assess thermal enhanced oil recovery and chemical flooding techniques.
To develop hard‑to‑recover reserves more rationally, KMG Engineering provided R&D assistance in implementing measures to enhance oil recovery and drain water, especially as regards low‑permeable layers such as fractured carbonate deposits of the Alibekmola field, undeveloped reserves of low‑permeability reservoirs of the Uzen field, and the Kenbay high‑viscosity oil. It conducted lab studies for chemical enhanced oil recovery (EOR), made various sector geological and hydrodynamic models, and selected the best options in terms of technical and economic parameters. In particular, KMG Engineering conducted tests to select optimal polymers for Kalamkas and Uzen. Pilots were launched to evaluate chemical compositions for profile modification at Kalamkas and waterproofing at several fields.
As part of the research, KMG Engineering tested chemical EOR methods for applicability at Uzen, identified high‑potential solutions and conducted a pre‑feasibility study followed by recommendations to further test potentially viable technologies.
To standardise approaches and methodology to assess EOR methods, standards for the feasibility study of EOR methods, oil production intensification and waterproofing during planning and testing are currently drafted for KMG’s oil producing subsidiaries.
To identify production bottlenecks and hampering factors, KMG Engineering classified such bottlenecks into technological and methodological groups, studied possible solutions and gradually integrated various R&D tools in production processes. Then the company made a review of technological bottlenecks and recommended solutions for key fields of KMG’s subsidiaries and associates and drafted detailed schedules to address these bottlenecks and improve EOR efficiency for the said fields.
January 2023 saw the launch of a pilot testing centre, an internet portal to improve communications between potential suppliers and KMG’s oil subsidiaries, streamline the procedure to present and assess new technologies, and keep all oil subsidiaries up to date on current and completed pilot tests of such techniques and innovations.
Oil refining and petrochemicals
To build new refining and petrochemical facilities and units, KMG leverages proven modern solutions designed by the leading foreign licensors using their proprietary licences and know‑how.
Based on the licences acquired by KMG, licensors develop a FEED project.
A FEED project comprises R&D, design and engineering process solutions, including hardware and controls to ensure products are made from the approved feedstock.
The FEED document contains data required to use the technology (if linked to specific conditions) as a process solution when drafting design documentation for construction.
The project to construct an LPG treatment facility at Pavlodar Refinery relies on a UOP (FEED project developer) technology – Merox. It is an efficient and cheap catalytic process to chemically treat hydrocarbon gases by removing sulphur in the form of mercaptans. The facility has an annual capacity of 100 thous. tonnes.
The project on reconstruction of the diesel hydrotreating plant including integration of a dewaxing unit at Pavlodar Refinery leverages Shell (FEED developer) technology to obtain winter diesel fuel with a cloud point of –28 °C (improvement by 20 °C) as well as K4 and K5 summer diesel fuel. The plant has an annual capacity of 160 thous. tonnes.
KPI Inc.’s polypropylene facility in the Atyrau Region takes advantage of Lummus Technology (FEED developer) processes for propane dehydrogenation (Catofin) and propylene polymerisation (Novolen PP process). A 500 ktpa facility uses cutting‑edge production technologies and equipment to make innovative products unique to Kazakhstan.
The technology is a continuous combined manufacturing method with fast processes and process flows (at temperatures from +5,900 °C to –1,500 °C) that can produce explosive mixtures (propane, propylene, ethylene, fuel gas and hydrogen). It is used for small‑scale production of customised grades (high‑refractive‑index, phthalate‑free, etc.)
A part of a complex manufacturing facility, the propane dehydrogenation plant with eight reactors has a short main reaction (24 minutes),with propane residence time in the reaction zone of the pyrolysis furnace of 0.2 seconds at 620 °C (pyrolysis intensity).
The facility also represents highly specialised critical production, with processes and hardware associated with a high risk of explosion (including critical operating parameters) and high hazard indicators.
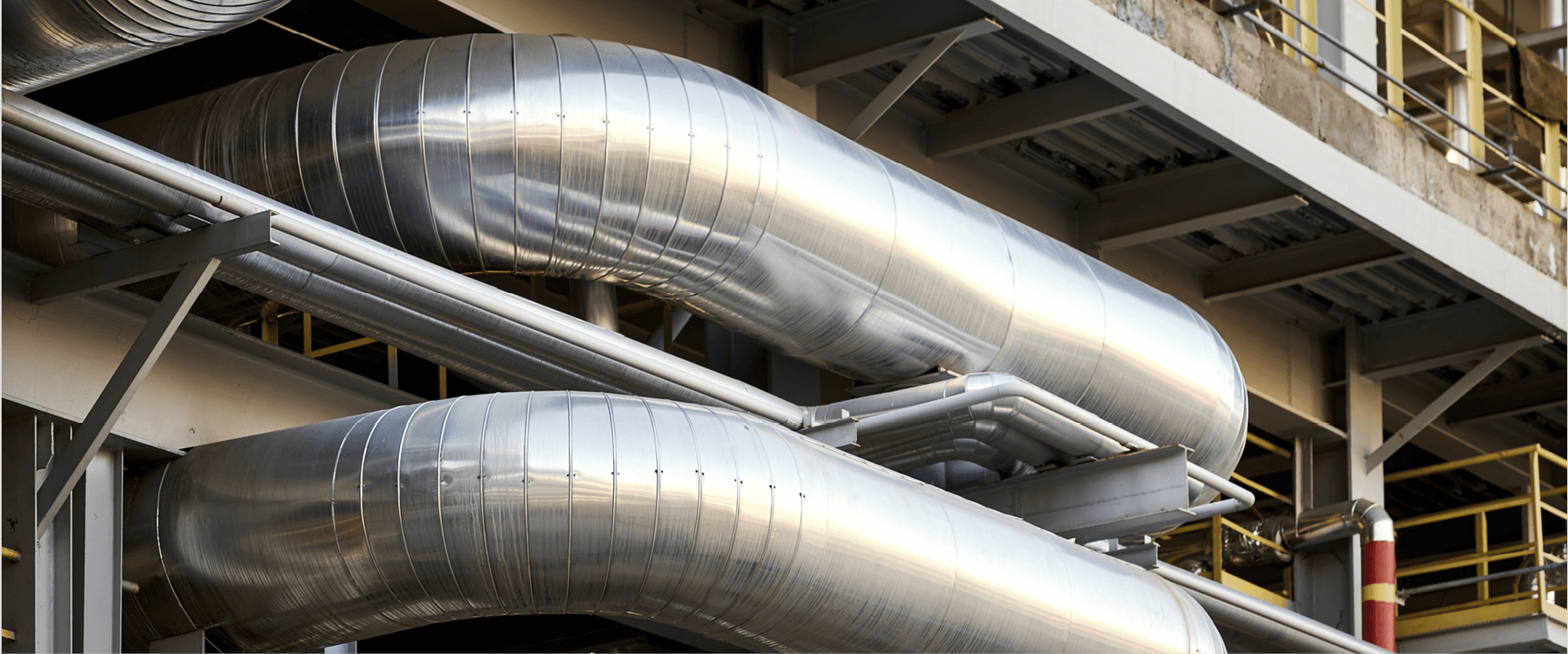
Engineering simulation at Kazakhstan refineries
In 2020, Kazakhstan refineries ran the first engineering simulation systems – software to create a digital twin of a process unit and select an optimal operating mode.
Atyrau and Pavlodar refineries created models of primary and key secondary oil refining processes.
Based on calculations made to optimise operating parameters, process units were running in a test mode between 2022 and 2023.
Atyrau Refinery streamlined the operation of a column at the AVT‑3 vacuum distillation unit by increasing its load by 10%. This helped improve the yield and sharpness of oil product separation, with an economic effect equal to KZT 500 mln in December 2023 and estimated at KZT 5 bln for the year.
While testing the calculations, Pavlodar Refinery achieved fuel savings equivalent to KZT 170 mln per year at its bitumen and atmospheric oil distillation units.
As part of a strategic initiative to address the rising demand for light oil products and to adjust Atyrau Refinery’s processes for Tengiz oil, Atyrau Refinery initiated the Efficiency Improvement project. The project will help implement advanced technologies at LG‑35–11/300–95 catalytic reformer, delayed coker unit and EDD‑ADU‑2 unit to boost the output of high‑quality fuels such as motor petrol, diesel, and LNG. These measures seek to increase production efficiency and eco‑friendliness, with emissions to be cut by 12% from the 2019 level by 2031. The project is expected to run between 2023 and 2027.
Advanced process control system
In 2020, the Company started to introduce an advanced process control (APC) system at Atyrau Refinery.
The APC system works as an autopilot to maintain the unit’s operation within set parameters. The system automatically controls the stability of loading parameters, temperature in columns and furnaces, and the quality of outgoing flows to increase oil product yield, reduce energy consumption, minimise human errors in process control, and boost product quality.
Similar control systems running at ADU‑2 and AVDU‑3 distillation units helped increase the yield of straight‑run petrol and kerosene and gasoil fractions by 0.3% and 0.43%, respectively, with an annual economic effect of KZT 1.2 bln.
In 2024, the system will be fully implemented at a gasoline hydrotreating and catalytic reforming unit at Atyrau Refinery and an oil refining unit of PetroKazakhstan Oil Products.
Efficiency improvement at Atyrau Refinery
As part of the strategic project to boost efficiency at Atyrau Refinery, KMG focused on upgrading and expanding production capacities to meet the demand for light oil products and refine oil from the Tengiz field. The project comprises eight subprojects, including the upgrade of LG‑35–11/300–95 catalytic reformer, an increase in LNG production, reconstruction of a delayed coker unit, installation of an extra compressor at the Prime D unit, EDD‑ADU‑2 upgrade, construction of a pumping station, and design of infrastructure for straight‑run naphtha processing. These steps seek to boost the output of quality oil products, streamline logistics and minimise environmental risks to deliver a 12% cut in GHG emissions from the 2019 level by 2031. Scheduled for 2023–2027, the project demonstrates Atyrau Refinery’s drive for innovation and environmental sustainability.
Production ramp‑up at Caspi Bitum
At present, KMG is considering the ramp‑up of Caspi Bitum refining capacities from 1 to 1.5 mln tonnes of oil per annum, with an annual road bitumen output potentially reaching 750 thous tonnes. This project will ensure the permanent availability of bitumen for road pavement domestically, including during road construction and reconstruction. On top of that, it will help substitute imports with local products and boost the country’s export potential. This is to be achieved through the upgrade of the existing EDD‑AVDU primary oil refining unit. The project is scheduled for 2023–2024. In the reporting year, a pre‑feasibility study of the Project was developed, a technical audit of the plant was carried out, and the FEED stage of the Project was approved by the KMG Investment Committee.
Developing professional competencies of KMG Group employees
- 1. An electronic library of production equipment and technical documents has been developed using QR codes to provide access to information at production sites.
- 2. Managers and officers in charge can take a 72‑hour Workplace Health and Safety course, including nine modules on key requirements.
- 3. Updated tests on industrial safety are available in two languages, and safety courses have been refreshed.
- 4. Videos on safety standards, the Tazalyq project and automated environmental monitoring information system have been prepared.
- 5. Modular educational programmes across five domains have been revised and updated to enhance field development competencies.
Hydrogen energy development
- 1. A feasibility study for low‑carbon blue hydrogen has been conducted and a derivative production blueprint developed.
- 2. KMG commenced to draft a water resource atlas to produce green hydrogen and are conducting negotiations with local and foreign institutions.
- 3. International standards for using metal hydride to store hydrogen were analysed and recommendations were issued to be included in the 2024–2027 National Standardisation Plan.
- 4. An international workshop on hydrogen energy has been organised to further educate employees of the Company and its subsidiaries and associates.
- 5. The Company held meetings with potential partners and signed a memorandum of understanding with Mitsubishi Heavy Industries.
- 6. KMG have drafted technical specifications, purchased equipment and conducted start‑up at a hydrogen research lab.
- 7. An article was published at International Journal of Hydrogen Energy.
- 8. Employees received training in hydrogen technologies under an international internship programme organised by Japan Cooperation Centre for Petroleum and Sustainable Energy.
Digital technology implementation
Control and analytics centre
In October 2023, KMG opened a new control and analytics centre (CAC), one of the most advanced globally. This is a digital platform to monitor and analyse all processes related to oil and gas production, transportation and treatment in real time.
The centre boasts a huge 4K LED video display occupying over 100 m2. Supplied and installed by Daktronics, a global leader in LED display manufacturing and integration, the display shows data, such as maps, charts, tables, and videos, from a variety of sources, including satellites, drones, sensors and cameras.
The control and analytics centre is equipped with excellent computing resources and AI to help make analytics‑ and forecast‑driven day‑to‑day and strategic decisions. It can process and store huge data volumes, while keeping them confidential and secure.
The centre is an important step in KMG’s digital transformation aimed at boosting efficiency, reliability and eco‑friendliness of its operations. The CAC is a driving force behind innovation and R&D in Kazakhstan’s oil and gas industry. Its employees working round the clock in any conditions show high professionalism and strong competencies.
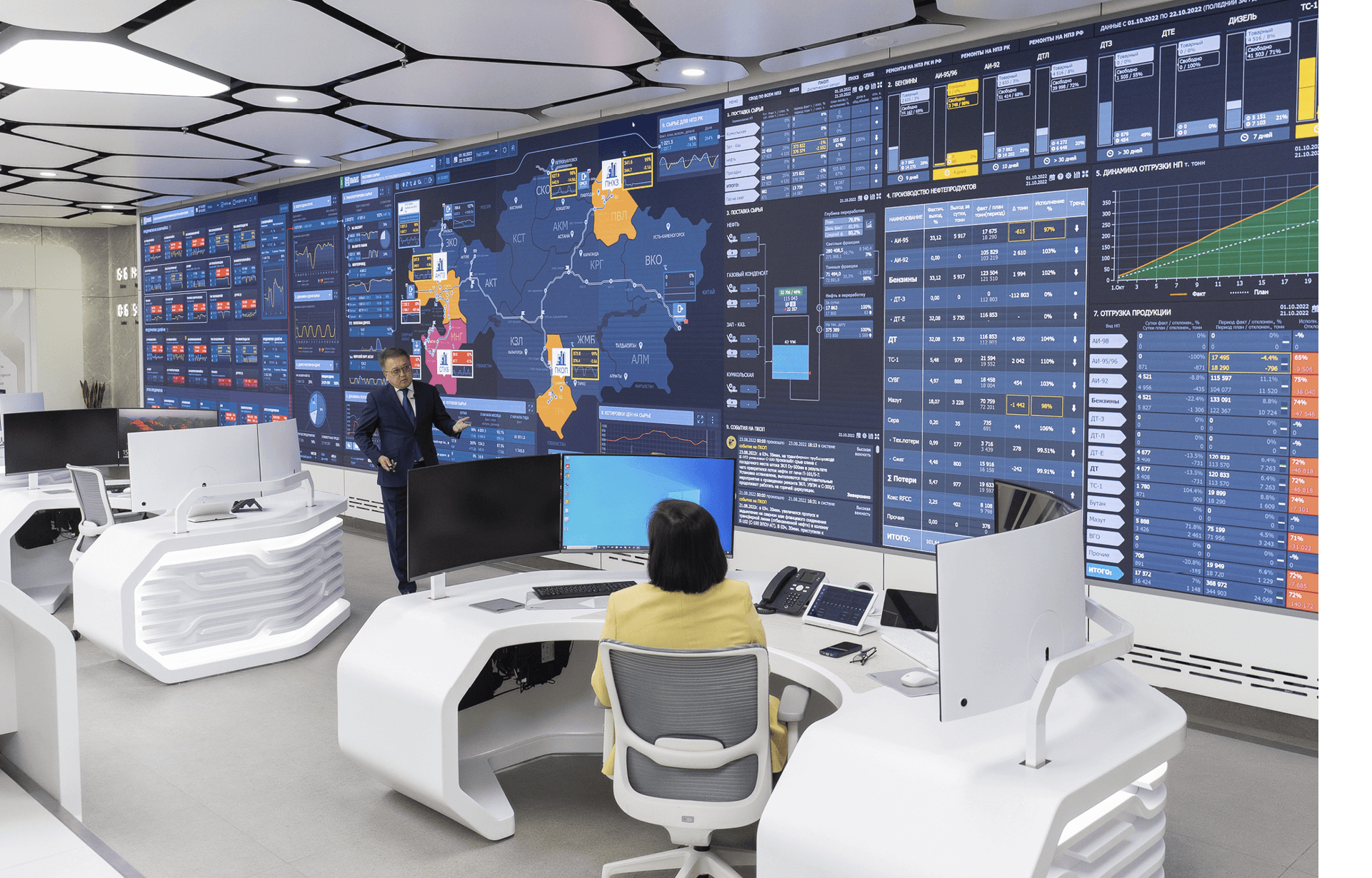